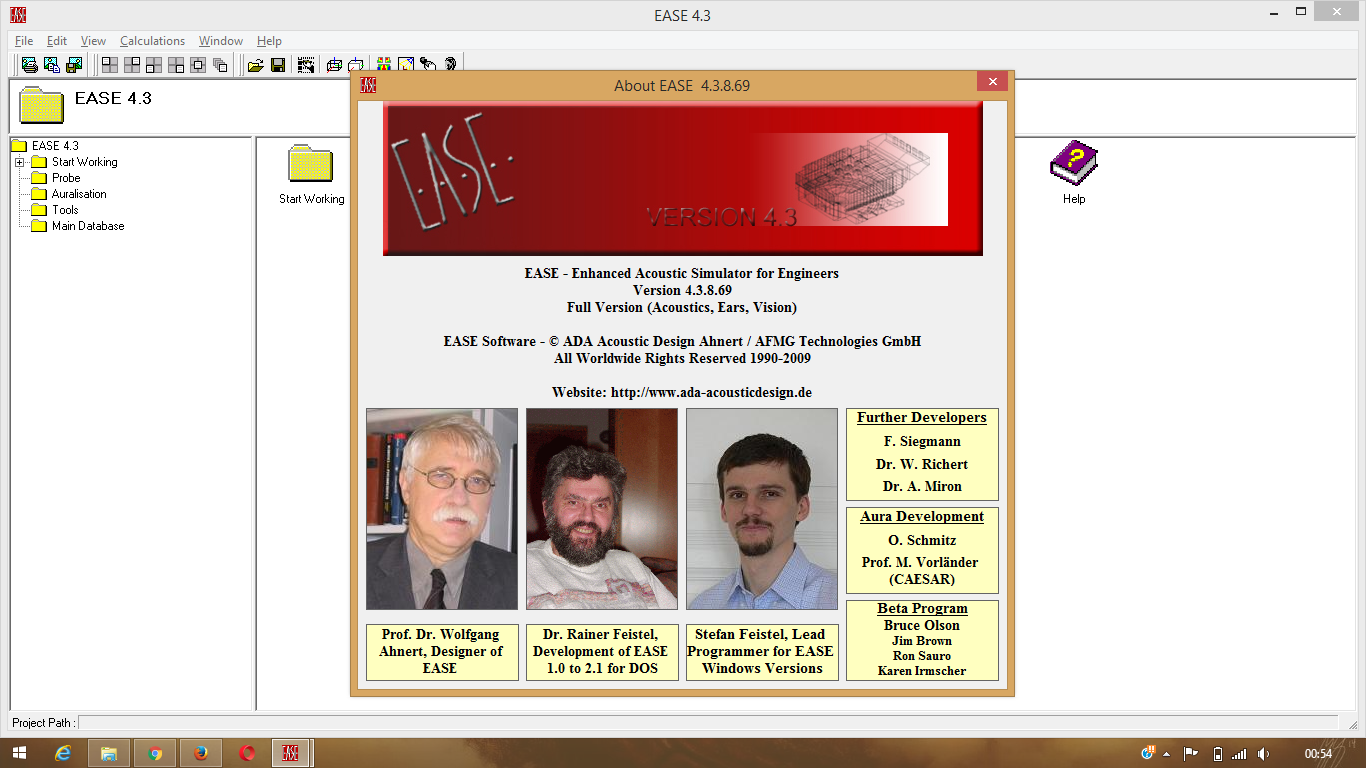

Jan 4, 2018 - “Our vision is that simulation will become as pervasive and as easy to use as Excel. Determines the transmission loss and acoustic pressure in a muffler. But as industry focuses on cracking the autonomous driving nut,. The EASE software suite provides system designers and consultants with an invaluable set of tools for all aspects of professional practice, from detailed, realistic modeling and simulation of venue acoustics and sound system performance to informative and engaging client presentations, as well as professional data assessment and verification.
• 682 Downloads • Abstract The aim of this study was to investigate the applicability of acoustic emission (AE) technique to evaluate delamination crack in glass/epoxy composite laminates under quasi-static and fatigue loading. To this aim, double cantilever beam specimens were subjected to mode I quasi-static and fatigue loading conditions and the generated AE signals were recorded during the tests. By analyzing the mechanical and AE results, an analytical correlation between the AE energy with the released strain energy and the crack growth was established. It was found that there is a 3rd degree polynomial correlation between the crack growth and the cumulative AE energy. Using this correlation the delamination crack growth was predicted under both the static and fatigue loading conditions. Kartinki raskraski fnaf.
The latest Tweets from Art (@NauPhotos). Photographer by night IT pro by day. Baza dannih magazina avtozapchastej.
The predicted crack growth values was were in a good agreement with the visually recorded data during the tests. The results indicated that the proposed AE-based method has good applicability to evaluate the delamination crack growth under quasi-static and fatigue loading conditions, especially when the crack is embedded within the structure and could not be seen visually. Fiber reinforced plastic composites (FRP) have many advantages such as high specific strength, specific stiffness, etc. However, these materials suffer from different damage mechanisms, such as matrix cracking, fiber breakage and delamination [,,, ]. The principal mode of failure in laminated composites is the separation along the interfaces of the layers, viz, delamination [,,,,, ]. This failure results in dramatic reduction of residual strength and stiffness of the structure.
Delamination occurs under different loading conditions, i.e. Mode I, mode II and mode III. However, mode I delamination is the most common mode of failure occurred in the structures. This is due to lower energy that is required for the initiation of mode I delamination [,, ]. Due to complexity of laminated composites, prediction of fatigue behavior in these materials is not straight forward [ ]. Accurate measurement of fatigue crack growth has become a challenging issue in fracture mechanics analyses.
Fatigue crack growth monitoring is a difficult and time-consuming test [ ]. In addition, work gets harder when the crack is embedded within the structure and could not be seen visually. Acoustic emission (AE) is a naturally occurring phenomenon, which is the result of transient elastic wave propagation caused by a sudden release of energy inside the material [ ]. There are various sources of AE events in composite materials such as matrix cracking, fiber/matrix debonding, fiber breakage, etc. Recently, AE has been utilized as an applicable technique to detect in-situ information from the damages that occur in laminated composites [,,,, ]. Some studies have used AE technique to investigate the delamination behavior under quasi-static loading condition [,,,, ].
- Author: admin
- Category: Category